GENERATIVE WHEEL DESIGN
In collaboration with software partner Autodesk, BAC produced revolutionary generative-design wheels for the new BAC Mono that once again play a major part in reducing the car’s weight. Generative design is a form of artificial intelligence that leverages cloud-computing to create better outcomes, allowing manufacturers to explore thousands of designs in less time than using traditional processes.
With BAC’s manufacturing constraints and functional requirements added to Fusion 360 software from the base of its revolutionary hybrid carbon-composite wheels, the team was able to explore ways to make the wheels lighter by using less materials but still bring a strong aesthetic.
The results produced a remarkably beautiful wheel centre that’s 35% lighter than before – saving 1.22kg of reciprocating, unsprung mass – at just 2.2kg. Overall, the front wheels weigh 4.7kg and the rears 4.9kg, a staggering measurement that once again contributes to lighter weight, enhanced performance and reduced emissions.
Such is the BAC ethos that the company isn’t satisfied with just that result and will continue to push the boundaries of what’s possible through generative design. Away from the wheels, heavier components on the car like bellhousing will soon come under the generative design microscope and provide a lighter solution – continuing to demonstrate how such innovation can be exploited further across the industry.
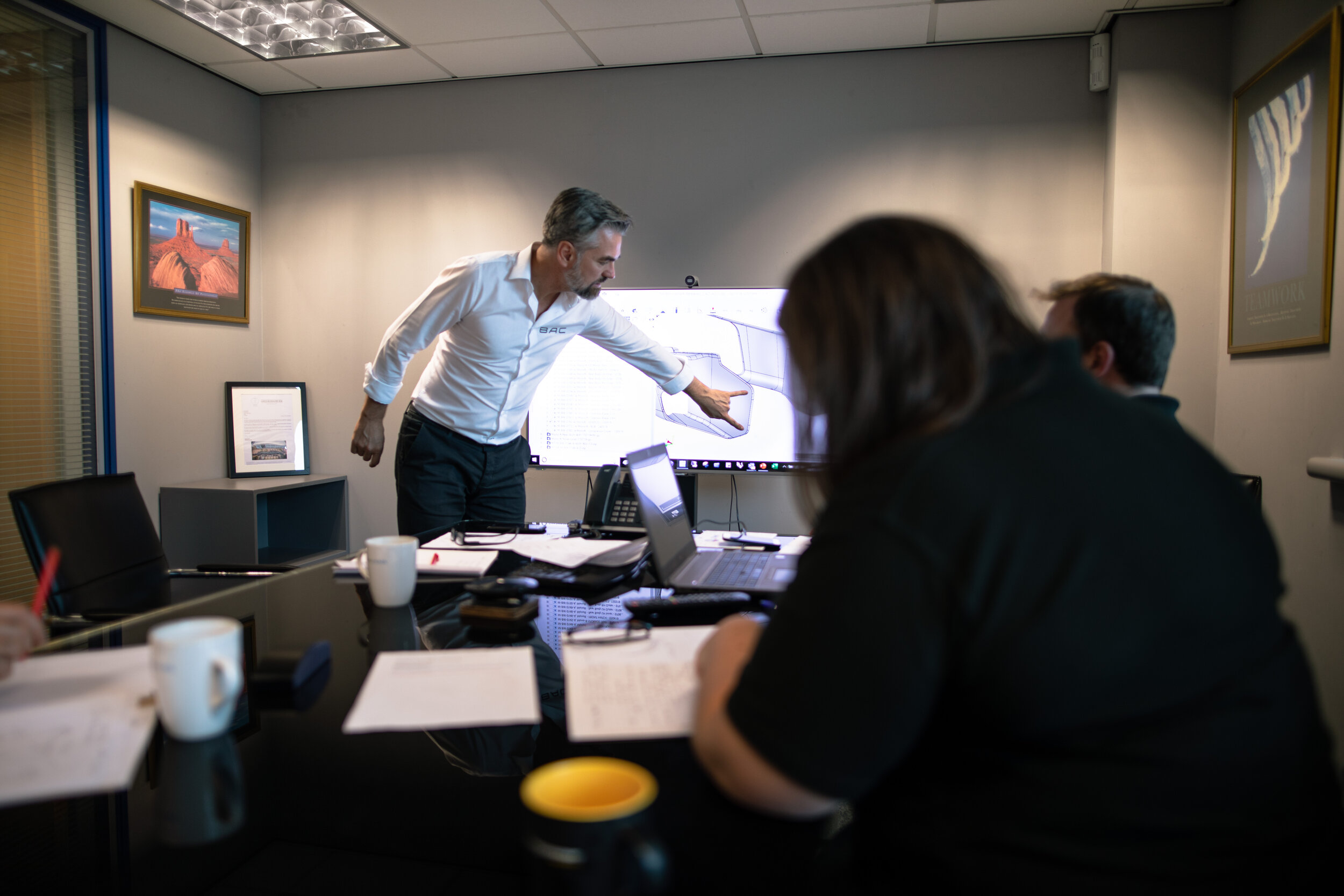
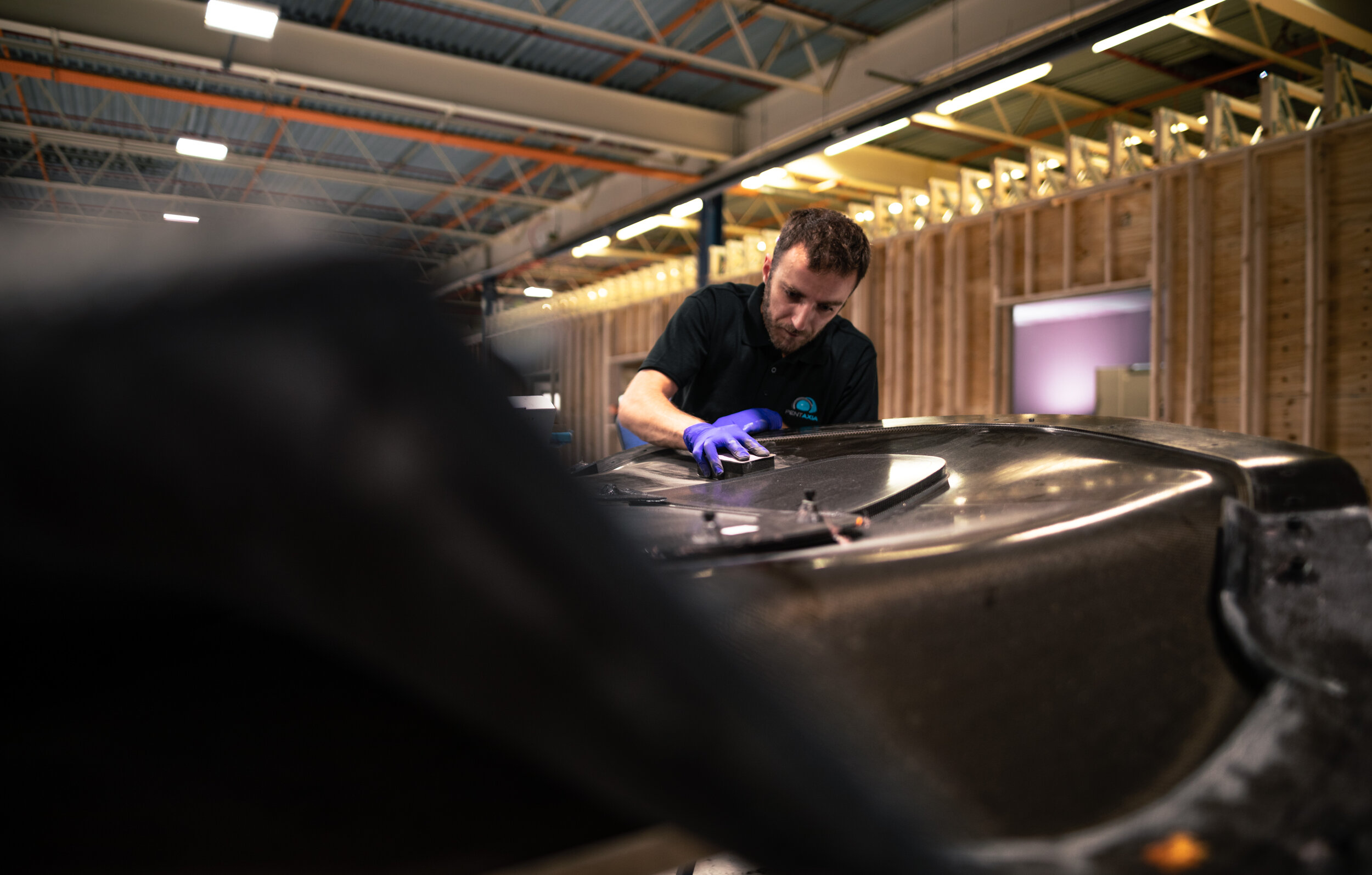
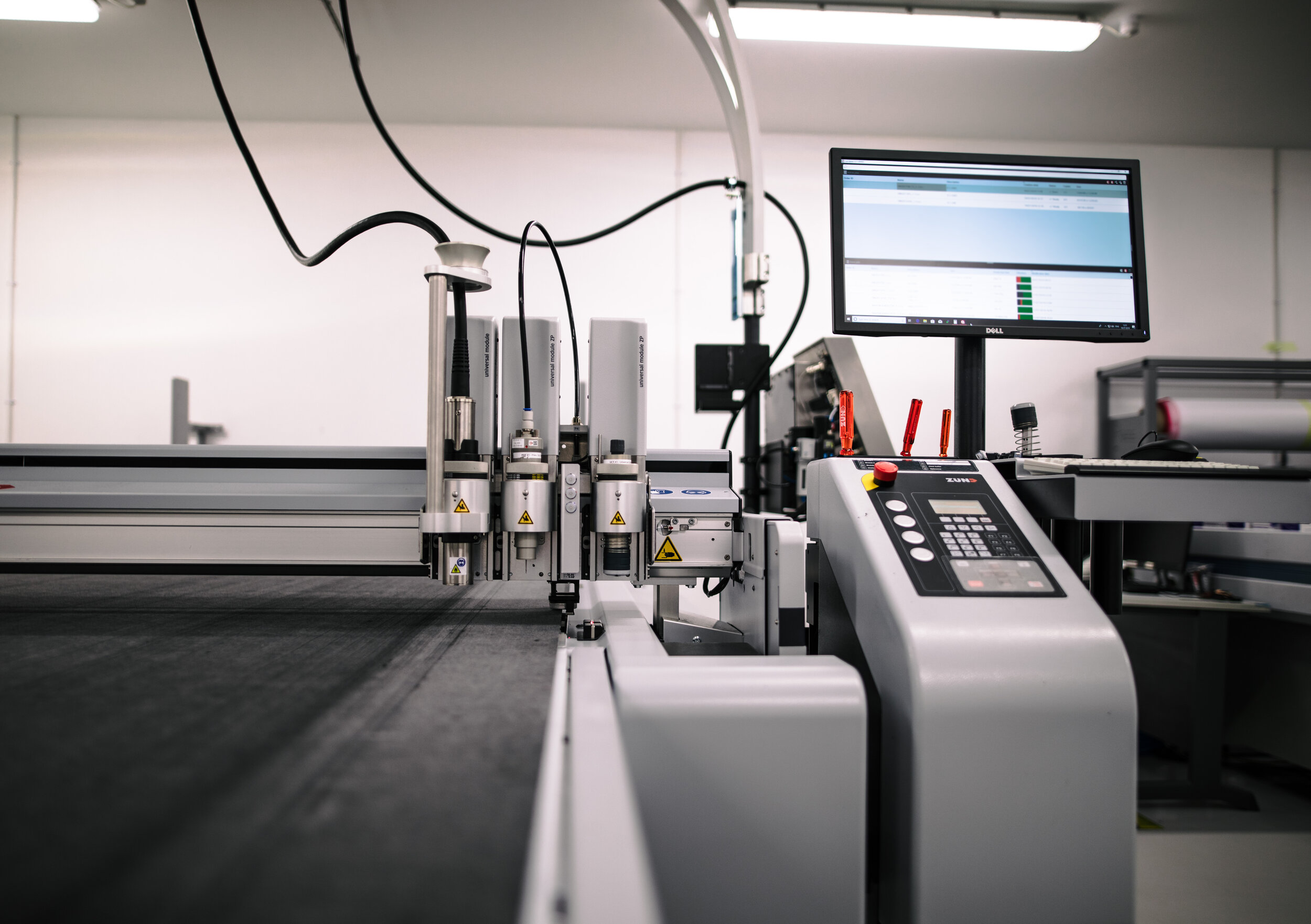
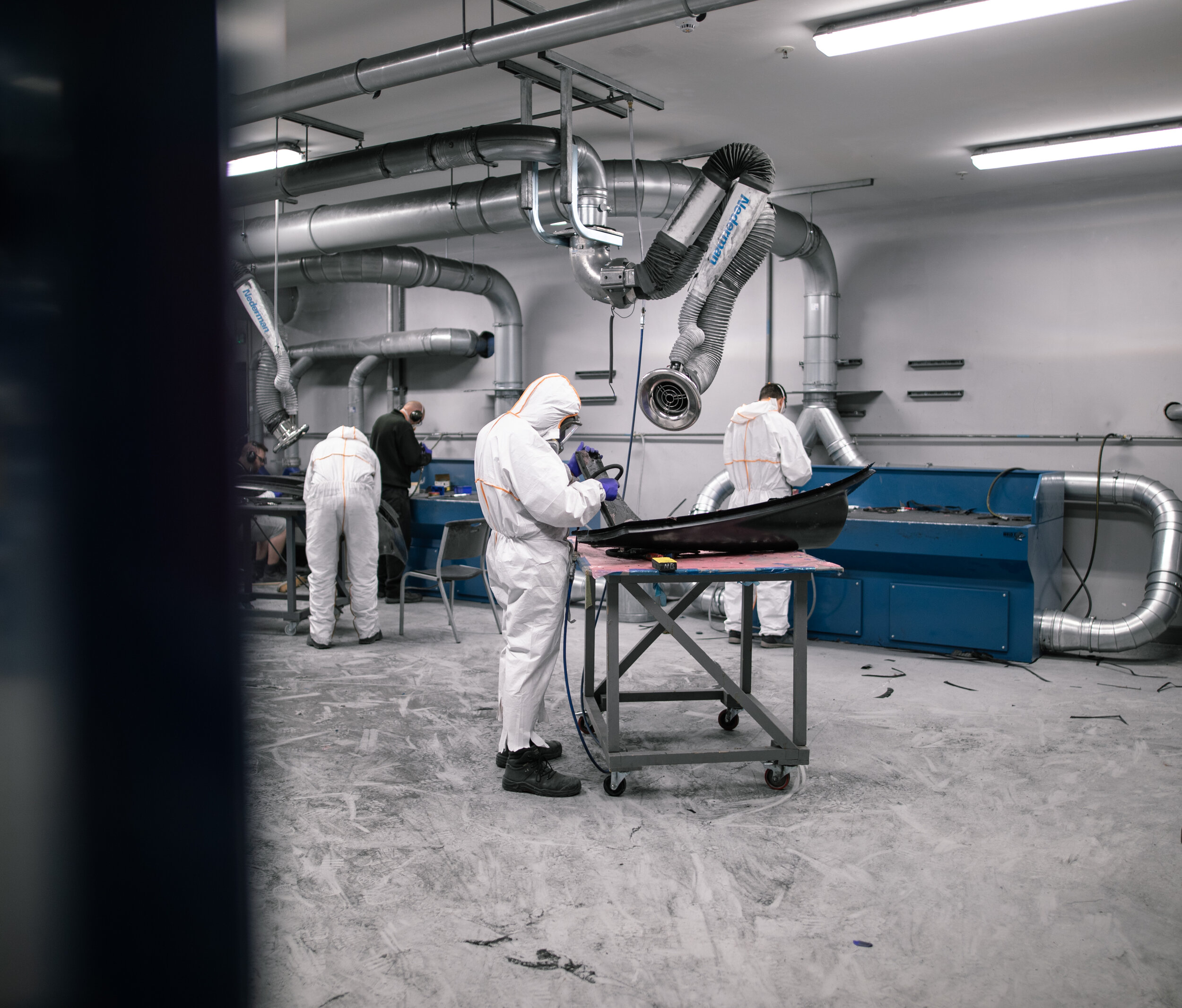
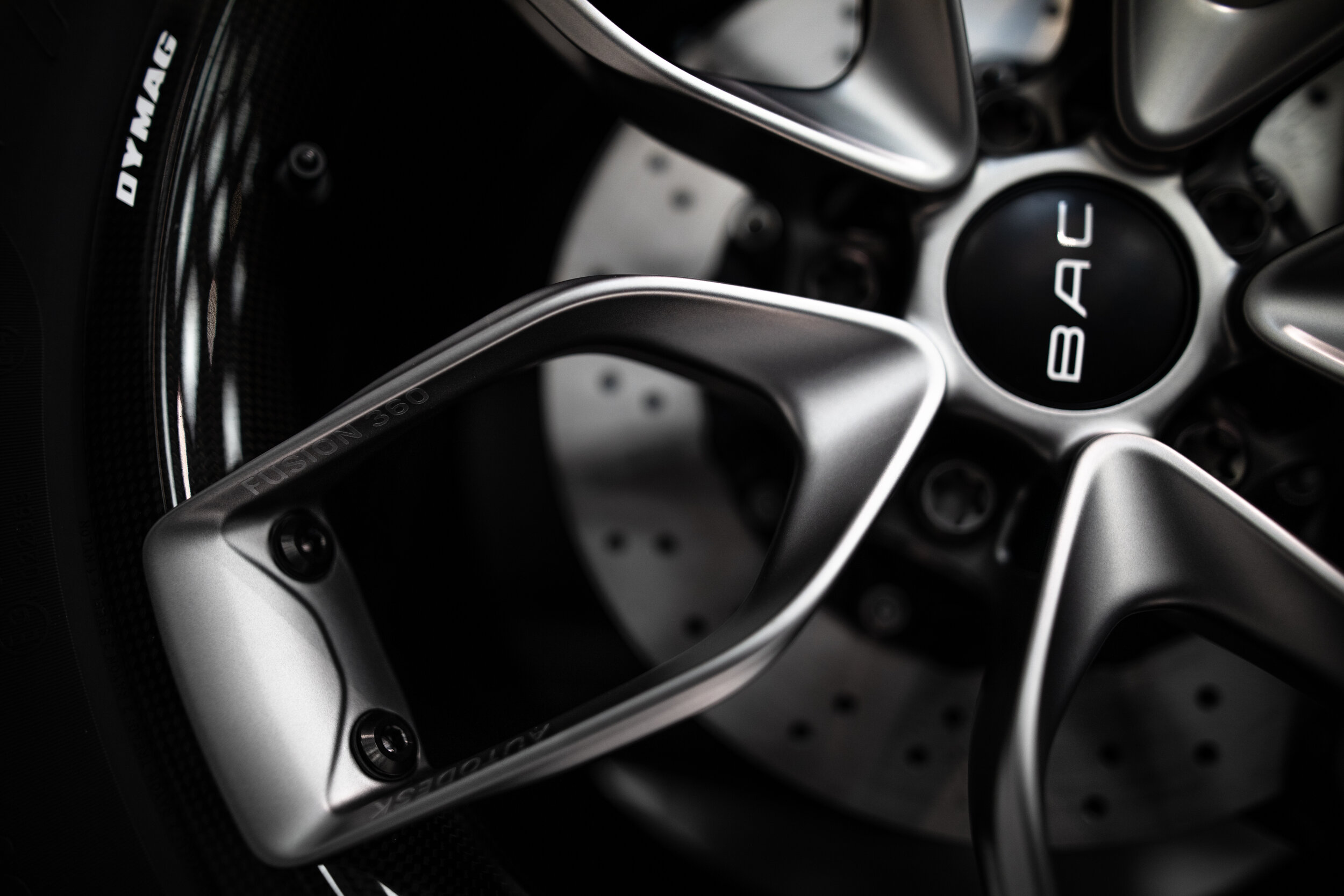
HYBRID CARBON-COMPOSITE WHEELS
In 2016, BAC broke ground technological ground once again when it became the first company in the world to develop hybrid carbon-composite wheels. Designed in collaboration with British performance wheel manufacturer Dymag, the 17-inch rims lowered the rotational weight of the wheel to bring about performance improvements and reduce emissions.
The total weight saving on the front axle is 23.5%, where the 7.5-inch by 17-inch wheels weigh 5.7kg each. The 9-inch-wide rear wheels each weigh 6.0kg, despite being half an inch wider than the standard rims, amounting to an overall 22.9% reduction in weight on the axle. Five pairs of titanium, Mono-branded bolts weigh 30.2g and save 212.5g per wheel.
ADDITIVE MANUFACTURING
Having explored the use of 3D printing with multiple components on the original Mono, BAC invested in bringing additive manufacturing in house and using the technology in series production for the first time with Mono R and the new BAC Mono.
Printing parts using high-performance, radical polymers (including Addigy® F1030 CF10, which features high heat deflection and excellent interlayer strength) on the state-of-the-art Ultimaker system in the BAC Innovation Centre successfully reduces design-to-manufacture timeframes of complex geometrical components. The BAC design team can successfully design, test and approve – or improve – parts in double-quick time before then utilising on Mono.
The use of additive manufacturing on the new Mono is more extensive than ever for BAC, with over 40 components being 3D printed, including the front and rear light surrounds, mirror arms and mirror housing, front hatch hinges, the front hatch latch mechanism, engine inlet components and more.
Not only does this reduce production timeframes dramatically, but it also further contributes to saving weight, reducing emissions and providing freedom for future improvements.